Ergonomic Risk Analysis Checklist
Below is a sample ergonomic risk analysis checklist that can be further developed for use for specific tasks and workplaces. Click on the links to open each of the 9 sections of the checklist.
- Is there lifting of loads, tools, or parts?
- Is there lowering of tools, loads, or parts?
- Is there overhead reaching for tools, loads, or parts?
- Is there bending at the waist to handle tools, loads, or parts?
- Is there twisting at the waist to handle tools, loads, or parts?
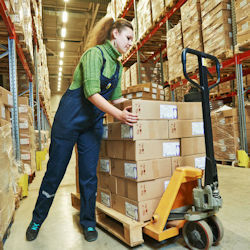
Does the job require bending, twisting, or moving heavy loads?
- Do tools and parts weigh more than 10 lb?
- Is reaching greater than 20 in.?
- Is bending, stooping, or squatting a primary task activity?
- Is lifting or lowering loads a primary task activity?
- Is walking or carrying loads a primary task activity?
- Is stair or ladder climbing with loads a primary task activity?
- Is pushing or pulling loads a primary task activity?
- Is reaching overhead a primary task activity?
- Do any of the above tasks require five or more complete work cycles to be done within a minute?
- Do workers complain that rest breaks and fatigue allowances are insufficient?
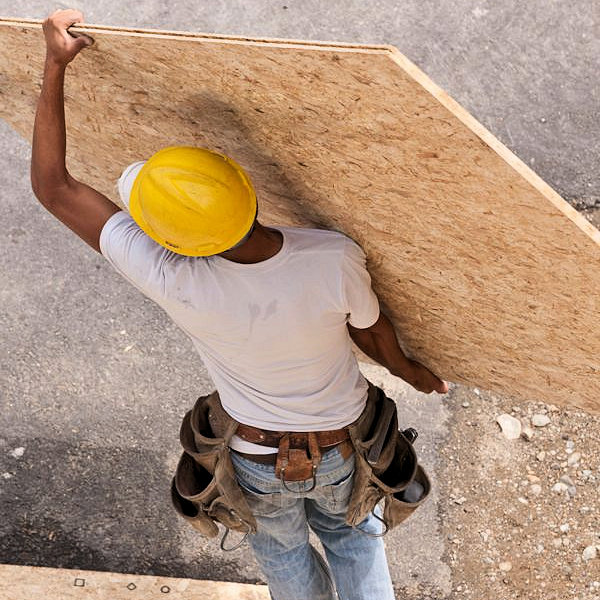
Lifting and carrying large heavy objects can cause MSDs.
- Do manual jobs require frequent, repetitive motions?
- Do work postures require frequent bending of the neck, shoulder, elbow, wrist, or finger joints?
- For seated work, do reaches for tools and materials exceed 15 in. from the worker's position?
- Is the worker unable to change his or her position often?
- Does the work involve forceful, quick, or sudden motions?
- Does the work involve shock or rapid buildup of forces?
- Is finger-pinch gripping used?
- Do job postures involve sustained muscle contraction of any limb?
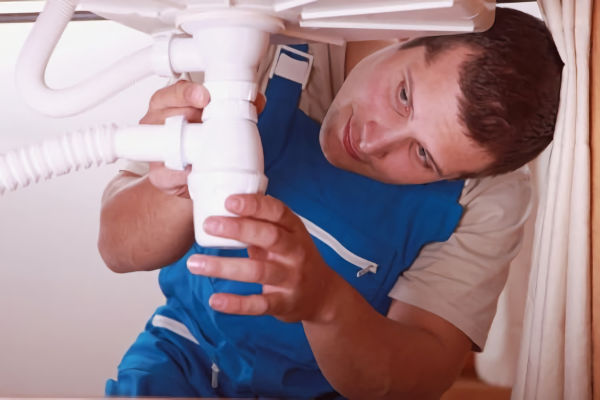
Does the job require an awkward posture?
- Do operators use computer workstations for more than 4 hours a day?
- Are there complaints of discomfort from those working at these stations?
- Is the chair or desk nonadjustable?
- Is the display monitor, keyboard, or document holder nonadjustable?
- Does lighting cause glare or make the monitor screen hard to read?
- Is the room temperature too hot or too cold?
- Is there irritating vibration or noise?
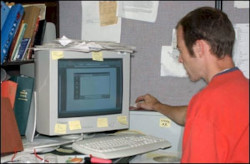
Does lighting cause glare or make the monitor screen hard to read?
- Is the temperature too hot or too cold?
- Are the worker's hands exposed to temperatures less than 70 degrees Fahrenheit?
- Is the workplace poorly lit?
- Is there glare?
- Is there excessive noise that is annoying, distracting, or producing hearing loss?
- Is there upper extremity or whole body vibration?
- Is air circulation too high or too low?
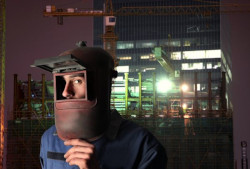
Is the workplace poorly lit?
- Are walkways uneven, slippery, or obstructed?
- Is housekeeping poor?
- Is there inadequate clearance or accessibility for performing tasks?
- Are stairs cluttered or lacking railings?
- Is proper footwear worn?
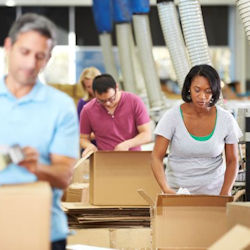
Is the workplace designed adequately for performing tasks?
- Is the handle too small or too large?
- Does the handle shape cause the operator to bend the wrist in order to use the tool?
- Is the tool hard to access?
- Does the tool weigh more than 9 lbs?
- Does the tool vibrate excessively?
- Does the tool cause excessive kickback to the operator?
- Does the tool become too hot or too cold?
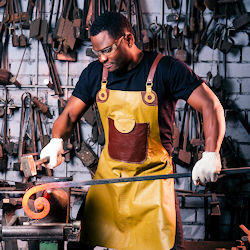
Does the task include the use of heavy tools?
- Do the gloves require the worker to use more force when performing job tasks?
- Do the gloves provide inadequate protection?
- Do the gloves present a hazard of catch points on the tool or in the workplace?

Does the use appropriate gloves for the job?
- Have workers been trained on best work practices?
- Is there little worker control over the work process?
- Is the task highly repetitive and monotonous?
- Does the job involve critical tasks with high accountability and little or no tolerance for error?
- Are work hours and breaks poorly organized?
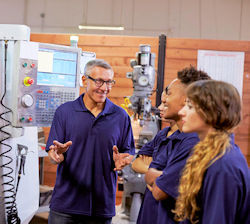
Are workers properly trained on ergonomic best practices?
This checklist was adapted from The University of Utah Research Foundation; Checklist for General Ergonomic Risk Analysis; available from ERGOWEB.