Abrasive Wheel Grinders
Abrasive wheel grinders come in many styles, sizes, and designs.
Typical bench and pedestal grinders often have two abrasive wheels, or one abrasive wheel and one special-purpose wheel such as a wire brush, a buffing wheel, or a sandstone wheel.
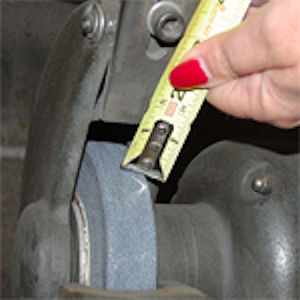
These grinders come with a safety guard covering most of the wheel, including the spindle end, nut, and flange projection. The guards must be strong enough to withstand the effects of a shattered wheel. A work rest and transparent shields are often included.
When using bench grinders:
- Grinders should have a protective guard and a properly adjusted tool rest with a gap within 1/8 inch between the grinding disc and the rest.
- The adjustable tongue guard on the top side of the grinder should be within 1/4 inch of the wheel.
- Ring test the abrasive wheel before they are mounted to ensure that they are free from cracks or other defects. Wheels should be tapped gently with a light, nonmetallic instrument. A stable and undamaged wheel will give a clear metallic tone or "ring."
- Employees using grinders should wear goggles and full-face shields. Keep these properly positioned near the bench grinder for ease of use.
- Locate an on/off switch (preferably a dead-man's switch) within reach of the person using the bench grinder.
- Only trained and competent workers should change grinding discs.
- The RPM rating of the grinding disk should match, or be greater than, that of the grinder rated RPM.
- Grinders should never be used to grind wood, plastics, or aluminum.
Knowledge Check Choose the best answer for the question.
3-2. What should be the gap between the grinding disc and the rest?
You forgot to answer the question!