Release from Lockout/Tagout
OSHA's Lockout/Tagout standard includes requirements for releasing machines or equipment that have been locked out or tagged out prior to restoring energy to the equipment and using it.
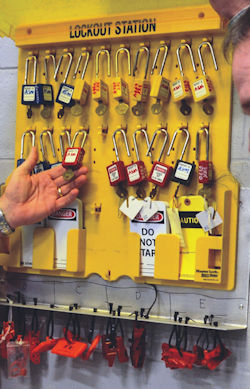
Before removing lockout or tagout devices and restoring energy, the authorized employee must follow these procedures:
- The work area must first be inspected to ensure that nonessential items (e.g., tools, spare parts) have been removed and that all of the machine or equipment components are operationally intact.
- The work area must then be checked to ensure all workers have been safety positioned or have cleared the area. In addition, all affected workers must be notified that the lockout or tagout devices have been removed before the equipment is started.
- Each lockout or tagout device must be removed from the energy-isolating device by the employee who applied the device.
- To make sure all lockout/tagout devices have been removed, inventory them when you return them to the lockout station.
Alternative Steps for Release from Lockout/Tagout
There are some things an employer must do if a worker who did not apply the lockout/tagout device actually removes the device. The person in charge must accomplish three actions listed below:
- Verify that the authorized employee who applied the device is not at the facility.
- Make all reasonable efforts to contact the authorized employee to inform him/her that his/her lockout or tagout device has been removed.
- Ensure that the authorized employee knows the lockout device has been removed before they resume work at the facility.
Knowledge Check Choose the best answer for the question.
3-8. Which step must be completed before restoring energy to equipment under lockout/tagout procedures?
You forgot to answer the question!