06.L.04 Mold Remediation.
If the assessment reveals mold remediation is required, then USAPHC TG 277, Army Facilities Management Information Document on Mold Remediation Issues , and any local, state, or host nation guidelines or regulations must be used.
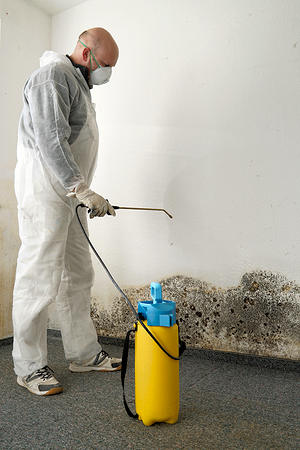
- A Mold Remediation Plan must be written by a competent mold expert and must include: location and extent of the mold, description of conditions found (i.e. wet or dry), type of materials or 'substrate' that the mold is growing on, whether the substrate will be cleaned or removed, source or problem which created the mold, repair of building structure or component that is the source, and whether the mold contaminated area will be isolated from the remainder of the building and or its occupants. The plan must also include the steps involved in remediation, identified hazards, recommended controls, equipment and materials (i.e., fungicide used for removal), inspection requirements and worker and occupant training requirements.
- Mold remediation should not be performed by the same entity that performed the mold assessment.
- Employees in the immediate area of the mold contamination must be informed of the remediation, results of any testing, and symptoms of the hazard. The employees must not be in the area during the remediation.
- Post-remediation air sampling must be done in the immediate area and in any areas in the mold spore or vegetative air-pathway and compared to outside air samples. Mold in areas above drop ceilings with combined air plenums must have air samples taken within the plenum as well as in air-serviced areas. Air samples should be taken in the immediate area of remediation and analyzed by a laboratory in the AIHA Environmental Microbiology Laboratory Accreditation Program
06.M Control of Chromium (VI) Exposure.
06.M.01 General.
All activities which could generate chromium (VI) fumes, mists, or dusts must be evaluated by an IH to determine potential personnel exposure over the OSHA Chromium (VI) standards. Typical operations where chromium exposures are high include: cutting or breaking up of cement surfaces made from Portland cement with a high chromium content, painting or paint removal operations, welding using rods or wire with a chromium coating, heating or welding on stainless steel, and handling or applying anti-corrosive substances or coatings.
- The evaluation must include a risk assessment of the type and frequency of exposure and breathing zone air samples and swipe sampling on surfaces in the work and surrounding area as described in 29 CFR 1910.1026.
- The evaluation must be added as an appendix to the APP or the Project SOH Plan. Individual sample results must be provided to the employee and add to their official occupational health record and a summary of the sample results should be posted in the work area.
06.M.02
To prevent exposure to chromium (VI), the use of paints with chromium pigments, Portland cement with greater than 20 ppm chromium, or chromium/arsenic treated lumber must be avoided when possible. Should chromium (VI) containing products be required, a justification and similar non-chromium (VI) product evaluation must be conducted and submitted for review by the GDA or the USACE SOHO.
06.M.03
If chromium containing compounds are used and the objective determination is inconclusive, before air sampling confirms the level of exposure, the employer must comply with the requirements of 1910.1026, 1915.1026, or 1926.1126, whichever is applicable. At a minimum, employers must provide appropriate PPE, respirators, decontamination facilities, and a lunch room/area clean from chromium dust and/or fume.
06.M.04
If air sampling confirms chromium (VI) exposure over the OEL, and there is no adequate substitute or work practice change (i.e., use of argon instead of carbon dioxide when arc welding), then the employer must provide appropriate engineering controls, i.e., local HEPA filtered ventilation systems, medical surveillance, housekeeping, and air sampling as required by the applicable chromium (VI) standard. If adequate engineering controls are not feasible or appropriate due to the length of the task, then PPE must be provided.
06.M.05
In areas where chromium (VI) is generated or used, there must be a housekeeping and decontamination program instituted.
- Employees must clean all surfaces a minimum of once a day or at the end of the shift that the chromium (VI) dust or fume was generated.
- At a minimum all exhaust and ventilation systems must be cleaned and filters changed annually.
- At a minimum, workers must remove outer work clothing before eating, drinking, or smoking.
06.N Crystalline Silica.
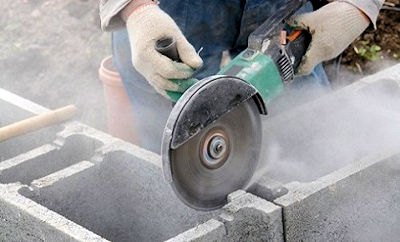
06.N.01 Occupational Standards.
- Employee airborne exposure to crystalline silica must not exceed the 8-hour time weighted average (TWA) OEL.
- Mandatory requirements.
- (1) Employee exposure must be eliminated through the implementation of feasible engineering controls.
- (2) After all such controls are implemented and they do not control to the OEL, each employer must rotate its employees to the extent possible in order to reduce exposure.
- (3) When all engineering or administrative controls have been implemented, and the level of respirable silica still exceeds OEL, respirators may be used in accordance with mandatory requirements of Section 5 E. and 29 CFR 1910.134.
- (4) Employees must be trained on the hazards of silica, the controls required to control the potential exposure, any sampling results and work practices to lower their exposure.
06.N.02 Monitoring.
- Each employer who has workplaces where silica is occupationally produced, reacted, released, transported, stored, handled, or used must inspect each workplace and work operation to determine if any employee may be exposed to silica at or above the OEL. This evaluation must be documented in the AHA for the job/task to be completed or PHA for government worker.
- Air monitoring and analysis. Sampling and analytical methods must be in accordance with those specified in Section 06.A.
Knowledge Check Choose the best answer for the question.
6-20. What is the employer to do if all engineering, administrative and work practice controls fail to lower exposure to chromium (and silica) below the occupational exposure limit (OEL)?
You forgot to answer the question!