16.D Inspection Criteria for Load Handling Equipment (LHE).
16.D.01 Inspections of LHE must be in accordance with this Section, applicable ASME standards, OSHA regulations and the manufacturer's recommendations.
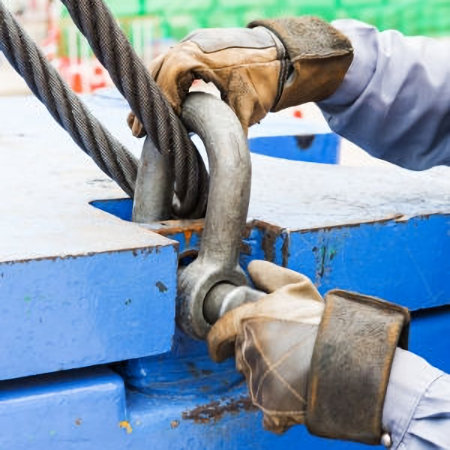
16.D.02 Records of all LHE tests and inspections must be maintained onsite. Contractors must make these records readily available upon request and, when submitted, they must become part of the official project file.
16.D.03 Contractor must provide the GDA 24-hours notice in advance of any LHE entering the site (prior to inspection/tests) so that observation of the Contractor's inspection process and spot checks may be conducted.
16.D.04 Whenever any LHE is found to be unsafe, or whenever a deficiency that affects the safe operation of the LHE is observed, the affected LHE must be immediately taken out of service and its use prohibited until unsafe conditions have been corrected.
16.D.05 Cranes, hoists, derricks and other LHE in regular service.
- Inspection procedures for LHE in regular service are divided into three general classifications based on the intervals at which inspections must be performed.
- The intervals depend on the nature of critical components of the LHE and the degree of their exposure to wear, deterioration, or malfunction.
- The three general types are: Shift, Monthly and Annual.
Note: Monthly inspections are required by OSHA. The items to be inspected and the requirements are the same as those covered by the Shift inspection, therefore monthly inspections will not be addressed separately in this Section but still must be performed.
16.D.06 Shift Inspections. Before every LHE operation (at beginning of each shift) or following a change of operator, a Competent Person (CP) must, at a minimum, visually inspect the items in accordance with this Section, applicable ASME standards, OSHA regulations and the manufacturer's recommendations. Equipment must not be used until this inspection demonstrates that no corrective action is required.
- The shift inspection must be documented and must include the results of the inspection, name and signature of the CP who conducted the inspection and the date of the inspection.
- Documentation must be maintained for a minimum of 12 months, or the life of the contract, whichever is longer.
16.D.07 Annual Inspections. Annual Inspections must be performed at least annually, or more frequently if recommended by the manufacturer, or if a load bearing or load controlling part or component has been altered, replaced or repaired. > See Section 16.F.02.b (1).
Note: Adding/removing counterweights is not considered load controlling/load bearing.
- Annual inspection must be done by a QP and will include operational testing to determine that the equipment as configured in the inspection is functioning properly.
- The inspection must be documented and must include items checked and results of inspection, name and signature of the person who conducted the inspection, and the date and this documentation must be retained until at least the next annual inspection occurs, 12 months, or the duration of the contract, whichever is longer.
- If any deficiency is identified, an immediate determination must be made by the QP as to whether the deficiency constitutes a safety hazard. If so, then the equipment must be removed from service until it has been corrected. If not yet a safety hazard, the QP may determine that the employer must monitor daily until the deficiency is corrected.
16.D.08 Inspection of cranes, derricks and other LHE not in regular use. Annual inspection must be performed if the equipment has been idle for 3 months or more. > See Section 16.D.07.
16.D.09 If LHE is involved in an incident or accident, an inspection must be conducted in accordance with the manufacturer's recommendations. If the manufacturer is no longer available, a RPE must be consulted and must determine the level of inspection required.
16.D.10 Running and Standing Wire Rope Inspection.
- Each Shift. A CP must perform this inspection each shift by visually inspecting all running ropes, counterweight ropes and load trolley (standing) ropes in accordance with this Section, applicable ASME standards, OSHA regulations and the manufacturer's recommendations. Visual inspection must concentrate on identifying apparent deficiencies in wire rope (running and standing). Opening of wire rope is prohibited and booming down is not required as part of this inspection.
- (1) The shift inspection must be documented and must include the results of the inspection, name and signature of the CP who conducted the inspection and the date of the inspection.
- (2) Documentation must be maintained for a minimum of 12 months, or the life of the contract, whichever is longer.
- Annual. At least every 12 months, wire ropes (running and standing) in use on equipment must be inspected by a QP in accordance with this Section, applicable ASME standard, OSHA regulations and the manufacturer's recommendations. Documentation is same as for Shift inspections above.
Knowledge Check Choose the best answer for the question.
16-6. What are the three types of crane, hoist, derrick and other LHE inspections?
You forgot to answer the question!