Evaluate and Improve the SMS
Monitor performance and progress: The first step in monitoring is to define indicators that will help track performance and progress. Employers, managers, supervisors, and workers should establish and follow procedures to collect, analyze, and review performance data.
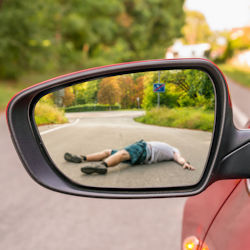
The two basic key performance indicators (KPIs) are "lagging" and "leading indicators."
Lagging indicators track past worker exposures and injuries, making them reactive measurements that focus on failures and impede improvement efforts. A few examples of lagging indicators include the:
- number and severity of injuries and illnesses,
- number of workplace hazards that go unreported, and
- workers' compensation data, including claim counts, rates, and cost
Leading indicators track how well various aspects of the program have been implemented and reflect steps taken to prevent injuries or illnesses before they occur. Consequently, they are considered "proactive" measurements. Leading indicators include the following:
Below are some suggested leading indicators for measuring the implementation of recommended practices for management leadership.
- Percentage of managers and supervisors who attend mandatory safety and health training for workers.
- Number of times each month that top management initiates discussion of a safety and health topic.
- Average score on survey questions related to workers’ perception of management’s safety and health commitment.
- Number of worker-reported hazards or concerns for which employers initiated corrective action within 48 hours (compared to the total number of such reports).
- Average time between worker report of a hazard or concern and management acknowledgement of the report.
- Number of safety-related line items in budget and percentage of these fully funded each year
Below are some suggested leading indicators for measuring the implementation of recommended practices for worker participation:
- Number of workers asked for feedback on good safety goals ahead of safety meetings.
- Number of workers involved in developing safety procedures.
- Number of workers participating in tool box talks.
- Number of workers participating in injury investigations.
- Safety perception survey participation rate.
- Number of workers involved in developing task-specific job safety analyses/job hazard analyses on how to perform routine tasks safely.
- Number of workers participating in accident investigation teams and helping to identify/implement corrective actions to eliminate hazards.
OSHA recommends using leading indicators for measuring change and making SMS improvements. See OSHA Publication 3970, Using Leading Indicators to Improve Safety and Health Outcomes.
Knowledge Check Choose the best answer for the question.
2-8. The number of accidents that occurred during the previous quarter would be considered an example of a _____ indicator.
You forgot to answer the question!